Introduzione
Checklab, collabora con una delle più importanti società italiane nel campo dei Controlli Non Distruttivi, Trattamenti Termici, Ispezioni e Collaudi di linee e impianti, Formazione e Consulenza in ambito saldatura, offrendo un’ampia serie di servizi, svolti da tecnici qualificati 2° e 3° Livello in accordo alle norme EN ISO 9712 e SNT-TC- 1A, supportati e garantiti da un Sistema di Qualità certificato ISO 9001:2015 e dall’Accreditamento come Laboratorio di prova secondo UNI CEI EN ISO/IEC 17025:2005.
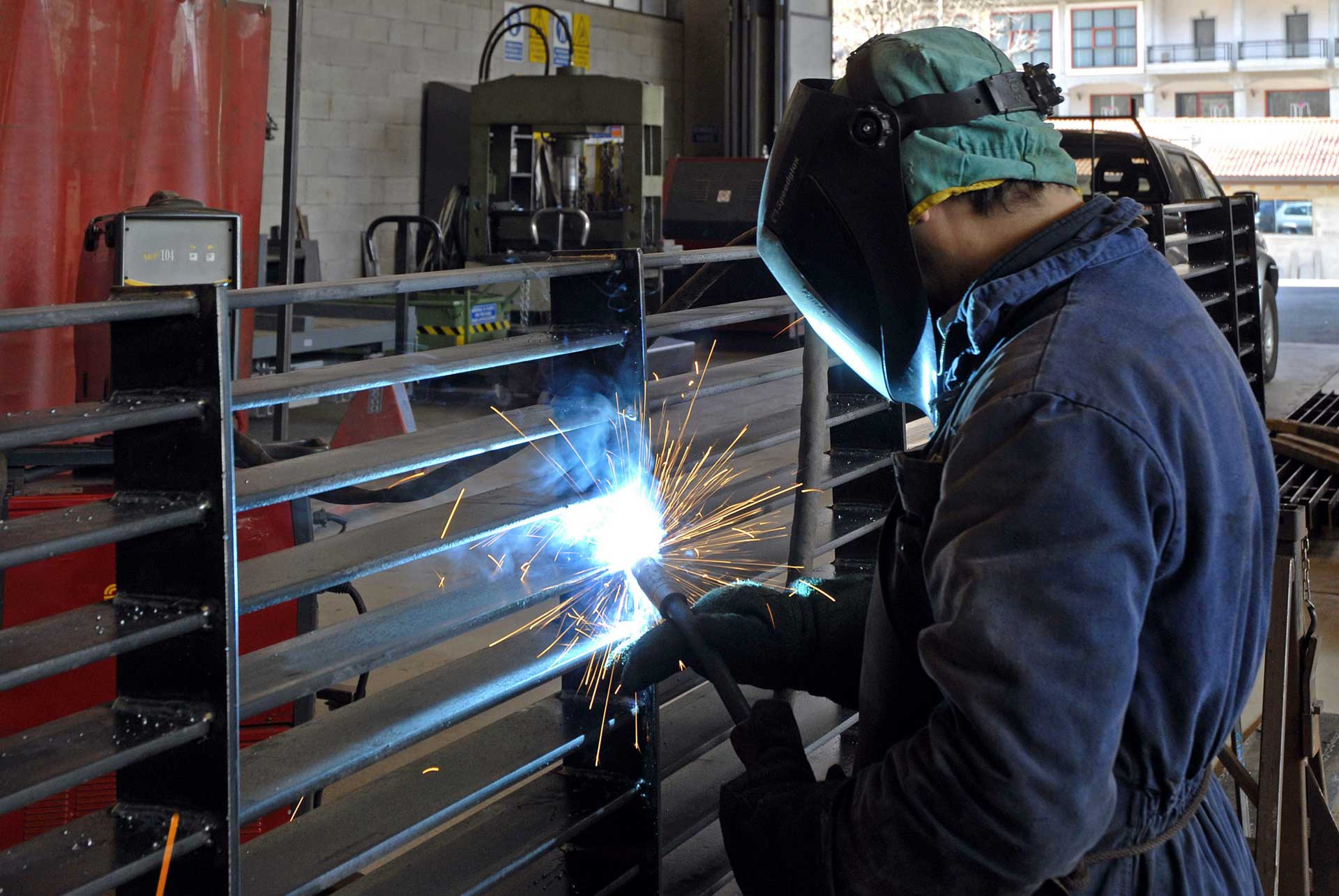
Saldatura
La criticità delle operazioni di saldatura viene gestita attraverso la definizione di opportuni parametri di esecuzione dei processi; la relativa documentazione richiede generalmente l’effettuazione di una serie di ispezioni durante tutte le fasi della costruzione, fino al completamento dei giunti saldati ed al loro controllo, sia in fabbricazione che in sede di montaggio finale. L’ispezione ha pertanto lo scopo di controllare la piena rispondenza delle modalità esecutive a quanto stabilito sui disegni e in fase di qualifica. Inoltre, nel corso dell’esecuzione delle saldature, l’ispettore ha modo di effettuare i primi e più immediati controlli diretti sui giunti, che già consentono in molti casi un efficace giudizio della qualità ottenuta. Poiché una buona ispezione aumenta l’affidabilità e la sicurezza della costruzione finita, è importante che essa venga eseguita da personale particolarmente qualificato.
Checklab dispone di ispettori di saldatura certificati sia dal TWI Certification come CSWIP, che dall’Istituto Italiano della Saldatura come International Welding Inspector (I.W.I.) , con consolidata esperienza nella costruzione di metanodotti e impianti industriali.
Grazie alla presenza di un International Welding Engineer (I.W.E.), che rappresenta il più alto livello di qualificazione previsto dall’EWF (Federazione Europea della Saldatura) e dall’IIW (Istituto Internazionale della Saldatura), Checklab offre ai propri clienti le principali attività di coordinamento della saldatura in accordo alla norma UNI EN ISO 14731:
- Il riesame del progetto e del contratto;
- La scelta ed il controllo dei processi di saldatura;
- La scelta dei materiali base e d’apporto;
- L’implementazione di opportuni sistemi di gestione;
- La verifica della corretta attuazione del processo di fabbricazione;
- L’emissione della documentazione di produzione: quaderno di saldatura (Welding Book), procedure di saldatura di produzione (WPS in accordo a EN ISO 15609 o ASME Sec. IX), piano di fabbricazione e controllo (PFC), ecc.
Considerata, inoltre, la vasta normativa di riferimento, Checklab eroga servizi di consulenza per l’attuazione e il soddisfacimento dei requisiti di numerose norme, tra cui:
- Famiglia delle UNI EN ISO 9692 sulla preparazione dei giunti;
- UNI EN ISO 13916 come guida sulla misurazione della temperatura del pre-riscaldo, interpass e post-riscaldo in saldatura;
- UNI EN ISO 17662 sulla taratura, verifica e validazione delle attrezzature usate per la saldatura;
- Famiglia delle UNI EN ISO 3834 sui requisiti di qualità per la saldatura per fusione dei materiali metallici;
- Famiglia delle UNI EN ISO 1090 per la marcatura CE dei componenti strutturali in acciaio e alluminio e relativi requisiti tecnici, ecc.
E’ evidente che la realizzazione di saldature esenti da difetti o, più realisticamente, il cui livello di qualità risulti riconducibile alle specifiche previste, è strettamente connessa all’impiego di una procedura adeguata al complesso delle caratteristiche del giunto e che l’esecuzione della stessa sia realizzata con le opportune tecniche. In caso contrario è assai probabile che la saldatura risulti poi affetta da gravi imperfezioni o da proprietà non adeguate al servizio, e che il giunto venga infine dichiarato inaccettabile.
Conseguentemente si rende necessario lo svolgimento di una serie di attività atte a validare le procedure di saldatura e a verificare che il personale operativo abbia la competenza necessaria allo svolgimento delle operazioni previste.
La qualificazione della procedura di saldatura consiste nell’identificazione di quei valori delle variabili essenziali che consentono l’ottenimento di un giunto saldato sano, con le caratteristiche metallurgiche necessarie all’impiego e le volute proprietà meccaniche, anticorrosione, estetiche, ecc.
La certificazione della procedura di saldatura è in sostanza una verifica che il materiale base, quello di apporto e la tecnica di saldatura utilizzati per effettuare il giunto saldato siano in grado di realizzare quanto il progetto si è proposto. Conseguentemente alle verifiche seguirà un verbale di qualificazione (WPQR – Welding Procedure Qualification Record o PQR – Procedure Qualification Record), che ha lo scopo di riportare i risultati delle prove e il campo di validità della certificazione, ossia l’intervallo dei valori per le variabili essenziali che risultano qualificati in base ai test eseguiti.
In collaborazione con i più prestigiosi organismi di certificazione accreditati, Checklab rilascia procedure di saldatura in accordo a:
- UNI EN ISO 15613 per prove di saldatura di pre-produzione su materiali metallici;
- UNI EN ISO 15614-1 per saldature ad arco e a gas di acciai e leghe di nichel;
- UNI EN ISO 15614-2 per saldature ad arco di alluminio;
- UNI EN ISO 15614-5 per saldature ad arco di titanio, zirconio e loro leghe;
- UNI EN ISO 15614-6 per saldature ad arco di rame e sue leghe;
- UNI EN ISO 15614-7 per riporto mediante saldatura su materiali metallici;
- UNI EN ISO 15614-8 per saldatura di tubi a piastra tubiera in materiali metallici;
- UNI EN ISO 15614-11 per saldatura a fascio elettronico e a fascio laser di materiali metallici;
- UNI EN ISO 15614-11 per saldatura a resistenza a punti, a rulli e a rilievi di materiali metallici;
- AWS D1.1, D.1.2, ecc. – Structural Welding Code;
- AWS B2.1 / B2.1M – Base Metal Grouping for Welding Procedure and Performance Qualification;
- Sezione IX del codice ASME “Boiler and Pressure Vessel Code”;
- UNI EN 13134 per la brasatura forte.
E’ quasi ovvio sottolineare il peso che gioca l’impiego di personale più o meno esperto nella buona riuscita delle saldature. Pertanto, la relativa qualificazione ha lo scopo di accertare che la mano d’opera impiegata possegga la necessaria abilità operativa.
Diversamente da quanto previsto per le procedure di saldatura, i criteri con cui vengono definite le variabili essenziali ed i relativi campi di validità sono basati su considerazioni di tipo operativo. Nel caso dei saldatori, il superamento della prova in determinate condizioni permette l’esecuzione della saldatura in condizioni operative più semplici utilizzando lo stesso processo di saldatura; nel caso degli operatori di saldatura, l’elemento determinante è il pannello di controllo dell’attrezzatura attraverso cui l’operatore inserisce i parametri.
Per ogni materiale base, quindi, vengono presi in considerazione i principali procedimenti di saldatura ed una serie di variabili essenziali, come ad esempio il rivestimento degli elettrodi, il gas di protezione, il tipo di flusso, il tipo di metallo d’apporto, lo spessore, il diametro e la posizione di saldatura.
Non è prevista una tipologia di saggio standardizzata, a meno delle misure di lunghezza, larghezza di tubi o lamiere: infatti, spessori e diametri dei saggi, in particolare, devono essere scelti in funzione delle esigenze produttive per le quali si effettua il processo di certificazione.
Checklab è in grado di fornire un valido supporto per l’individuazione delle qualifiche più idonee alla realtà produttiva della specifica azienda, evitando l’emissione successiva di più patentini con conseguente risparmio di tempo e costi. Tramite la certificazione finale emessa da noti enti accreditati di terza parte, si possono rilasciare qualifiche saldatori con elettrodi rivestiti (basico, acido, rutilico, cellulosico ,ecc.), con filo (pieno, animato, contenente flusso, metal cored, ecc.) in gas inerte (MIG), attivo (MAG) o senza gas protettivo, con elettrodo infusibile di tungsteno (TIG), con fiamma ossiacetilenica secondo:
- UNI EN ISO 9606-1 per acciai;
- UNI EN ISO 9606-2 per alluminio e sue leghe;
- UNI EN ISO 9606-3 per rame e sue leghe;
- UNI EN ISO 9606-4 per nichel e sue leghe;
- UNI EN ISO 9606-5 per zirconio e sue leghe;
- UNI EN ISO 14732 per operatori di saldatura e dei preparatori di saldatura per la saldatura completamente meccanizzata ed automatica di materiali metallici;
- UNI EN 13067 per assiemi saldati di materiale termoplastico;
- UNI 9737 per procedimenti ad elementi termici per contatto con attrezzatura meccanica e a elettrofusione di tubi e raccordi in polietilene per il convogliamento di gas combustibili, di acqua e di altri fluidi in pressione;
- UNI EN ISO 13585 per brasatori e operatori per la brasatura forte;
- AWS 1.1/D1.1M – Structural Welding Code;
- Sezione IX del codice ASME “Boiler and Pressure Vessel Code”.
I corsi erogati da Checklab sono la risposta alle esigenze formative specifiche per le aziende. La formazione può essere erogata in aula o direttamente presso i clienti, permettendo di sviluppare le competenze indispensabili al ruolo e di acquisire tutti gli strumenti necessari per accrescere la propria professionalità.
I docenti sono esperti, auditor e trainers, che oltre ai requisiti previsti per legge possiedono una comprovata esperienza operativa, che consente loro di dare un approccio pratico e vicino alle esigenze dei partecipanti ai corsi.
I materiali didattici sono elaborati per essere un utile strumento guida e vengono forniti per mezzo di slide a colori utilizzate durante le lezioni. Per alcuni percorsi formativi sono previsti esami finalizzati alla certificazione della competenza acquisita e viene rilasciato un attestato di partecipazione ad eventuale superamento del test finale.
Principali corsi attivati per l’anno corrente:
- Corso di Coordinatore della Saldatura (Welding Coordinator)
Il Welding Coordinator è una figura professionale esperta in saldatura dedicata alle attività di carattere organizzativo, esecutivo, di supervisione e di ispezione secondo quanto definito dalla norma EN ISO 14731. Il suo principale compito è quello di agevolare l’operatività dei processi per il rispetto dei requisiti minimi prefissati, gestendo gli esecutori materiali dei processi di saldatura e gli operatori delle prove non distruttive.
L’obiettivo del corso è di fornire una formazione specialistica per le figure professionali preposte alle attività di Welding Coordination, in modo da approfondire tutte le attività ed i compiti tipici del coordinatore di saldatura, tra cui: la corretta gestione di processi relativi ai Sistemi di Gestione della Qualità in saldatura; il riesame del contratto; il riesame del progetto; la concezione e progettazione delle giunzioni saldate; la pianificazione delle attività produttive; la gestione delle problematiche attinenti l’igiene e la sicurezza in saldatura; la gestione della movimentazione e dello stoccaggio di materiali e delle apparecchiature; la valutazione dell’idoneità all’uso di macchine e materiali; l’applicazione ed implementazione di norme, codici e disposizioni legislative inerenti le costruzioni saldate; la gestione dei controlli e dei collaudi per la verifica dell’idoneità all’esercizio; l’emissione, la gestione e l’archiviazione della documentazione.
- Corso per qualifica (patentino) di saldatore
La mansione del saldatore richiede lo sviluppo di una adeguata manualità e la conoscenza della tipologia di prodotto realizzato e delle relative prassi esecutive. Per questo motivo Checklab organizza una serie di corsi mirati a fornire le conoscenze di base per svolgere queste attività, lasciando eventualmente la possibilità d’integrazione con formazione personalizzata.
Checklab offre dunque un percorso formativo per l’ottenimento delle competenze di base attraverso un corso di carattere prevalentemente pratico indicato per chi desidera avvicinarsi alla mansione di saldatore senza avere esperienza pregressa, o per chi voglia perfezionarsi e conseguire una certificazione riconosciuta a livello nazionale ed internazionale.
Sono possibili corsi su saldatura ad elettrodo, a filo, a TIG e al cannello ossiacetilenico.
Controlli non distruttivi (CND)
L’Esame Visivo (VT) è stato applicato da sempre, essendo basato sulla percezione della vista nello svolgimento delle svariate attività umane, e in questo senso rappresenta il capostipite fra i C.N.D In generale, il controllo visivo ha lo scopo di ottenere un’analisi qualitativa e dimensionale del manufatto seguendo specifici criteri di accettabilità, la cui valutazione deve essere di tipo strumentale per un accurato dimensionamento delle imperfezioni. L’esame può essere svolto in modalità diretta (ad occhio nudo e/o tramite lenti d’ingrandimento) o remota (con l’ausilio di specchi, endoscopi, fibre ottiche e telecamere), a seconda delle condizioni di accessibilità delle superfici da ispezionare o in base alla necessità di registrazione. Spesso il VT precede o viene eseguito contemporaneamente ad altre prove, e risulta fondamentale per una più corretta interpretazione dei risultati. Benché possa sembrare il più semplice dei C.N.D. almeno dal punto di vista degli strumenti, richiede una solida esperienza, continua formazione e certificazione riconosciuta del personale addetto.
I controlli visivi vengono eseguiti da Checklab con la massima competenza, in accordo a norme Europee (EN ISO 17637, EN ISO 5817, EN 1370, EN 13100-1, ecc.) e a codici Americani (ASME Sec. V, ASME Sec. VIII, ASME B16.5, API 617, API 618, ecc.).
Il metodo di controllo non distruttivo con liquidi penetranti (PT) è fondamentalmente basato sull’esame visivo della superficie dopo l’applicazione, in sequenza, di un prodotto penetrante avente elevate caratteristiche di bagnatura delle superfici, e di un rivelatore, che ha il compito di esaltare il contrasto. In sostanza, il metodo rende visibili discontinuità affioranti in superficie, che potrebbero essere difficilmente distinguibili o addirittura del tutto non visibili dall’occhio umano.
VANTAGGI:
- Relativa facilità d’uso;
- Applicabile a numerosi tipi di materiale;
- Ampie superfici ispezionabili;
- Possibilità di controllare pezzi a geometria complessa;
- Indicazioni visibili direttamente sulla superficie del pezzo;
- Estrema flessibilità dei prodotti;
- Costo relativamente contenuto del controllo.
SVANTAGGI:
- Rilevabili solo discontinuità affioranti in superficie;
- I materiali devono presentare superfici non porose;
- La pulitura preliminare è una fase critica, poiché la presenza di inquinanti può compromettere l’esito;
- Sono necessarie varie fasi da procedurare al fine di garantire la massima ripetibilità dei risultati;
- Impiego di prodotti che possono risultare nocivi o dannosi per contatto, inalazione, ingestione;
- Talune lavorazioni superficiali prima del controllo possono diminuire la sensibilità d’esame.
Checklab dispone di tutte le attrezzature necessarie ad eseguire il controllo con liquidi penetranti sulle applicazioni più diversificate, sia in modalità a contrasto di colore che in fluorescenza, seguendo scrupolosamente riferimenti normativi Europei (EN ISO 3452-1, EN ISO 23277, EN 1371-1, EN 1371-2, EN 10228-2, EN 10246-11, ecc.) e Americani (ASME Sec. V, ASME Sec. VIII, ASTM E 165, ecc.).
Il principio del metodo di controllo con particelle magnetiche (MT) sfrutta la capacità di alcuni materiali, detti ferromagnetici, di attrarre altri materiali o sé stessi. Al pezzo in esame è applicato un intenso campo magnetico, ottenuto mediante un’apposita attrezzatura. Qualora fossero presenti discontinuità superficiali o subsuperficiali, esse interromperebbero le linee di flusso magnetico, creando una fuga di flusso localizzata rilevabile attraverso l’applicazione di particelle ferromagnetiche pigmentate.
VANTAGGI:
- Si possono rilevare discontinuità sulla superficie o appena al di sotto di essa;
- Pezzi di forma complessa possono essere controllati con semplicità;
- La pulitura preliminare delle superfici è meno critica rispetto ad altri metodi (ad esempio i PT);
- Il metodo è rapido e le indicazioni risultano visibili direttamente sulla superficie;
- I costi sono complessivamente contenuti;
- Le attrezzature portatili consentono notevole flessibilità nel caso di controlli in campo.
SVANTAGGI:
- Il metodo è inapplicabile su materiali non ferromagnetici (numerosi acciai inossidabili, leghe di Al, Mg, Ti, Cu, Ni o altri);
- Per controlli in posizione devono essere utilizzati rivelatori idonei;
- In alcuni casi può essere necessario rimuovere verniciature o strati protettivi superficiali per raggiungere la desiderata sensibilità di controllo;
- La capacità di rilevare discontinuità subsuperficiali è limitata;
- E’ fondamentale l’orientamento tra il piano della discontinuità e la direzione del campo magnetico.
Checklab conduce controlli MT utilizzando rilevatori secchi e in sospensione, con possibilità di variare le tipologie di magnetizzazione e in condizioni di visione sia fotopiche che scotopiche.
Le norme di riferimento possono essere di origine Europea (EN ISO 17638, EN ISO 23278, EN ISO 9934-1, EN 1369, EN 10228-1, EN 10246-12, ecc.) o Americana (ASME Sec. V, ASME Sec. VIII, ASTM E709, ASTM E1444, ecc.).
Il metodo radiografico impiega un fascio di radiazioni ionizzanti dirette verso il particolare da esaminare per evidenziarne discontinuità superficiali e interne. Parte delle radiazioni sono assorbite dal materiale attraversato in funzione delle proprie caratteristiche chimico-fisiche. In corrispondenza di discontinuità, l’assorbimento risulta differente e crea un contrasto rispetto al materiale circostante su un opportuno mezzo di rilevazione.
Le due tipologie di sorgente radiogena più diffuse sono:
- I radioisotopi, sostanze rese radioattive in modo artificiale allo scopo di ottenere un’emissione continua di raggi γ (gamma) di energia costante ed intensità decrescente nel tempo;
- I tubi radiogeni, macchine elettriche che seguono i principi di funzionamento del tubo di Coolidge (tubo catodico sottovuoto) ed emettono raggi X di energia ed intensità regolabili.
VANTAGGI:
- Tecnica applicabile a numerosissimi materiali;
- Consente l’ispezione di componenti anche assemblati;
- Ridotta preparazione delle superfici;
- Consente di rilevare variazioni di spessore, stati di corrosione, porosità, cricche, variazioni di densità del materiale;
- Fornisce un report permanente (pellicola radiografica o lastra).
SVANTAGGI:
- Il metodo risulta oneroso sul piano della gestione della sicurezza;
- L’addestramento degli operatori è complesso;
- Il pezzo deve essere accessibile da entrambi i lati;
- La giacitura della discontinuità è critica;
- A meno di tecniche specifiche, non è possibile determinare la profondità delle discontinuità;
- I costi sono significativi.
Il metodo radiografico viene applicato in quasi tutti i settori in cui Checklab opera, grazie al possesso di Decreto Ministeriale per il trasporto su strada di sostanze radioattive su tutto il territorio nazionale e di Decreto Prefettizio per la detenzione e l’impiego di sorgenti radiogene.
L’azienda dispone di radioisotopi di Iridio (Ir-192) e Selenio (Se-75) e di tubi radiogeni di varie potenze, che vengono impiegati nelle più svariate applicazioni in accordo a norme Europee (EN ISO 5579, EN ISO 17636-1, EN ISO 10675, EN ISO 4993, EN 12681, ecc.), Americane (ASME Sec. V, ASME Sec. VIII, ASTM E94, ASTM E155, ASTM E186, ASTM E446, ecc.) o a specifiche di clienti (SAL SNAM, ecc.).
Il controllo UT sfrutta la propagazione di onde ultrasonore all’interno del pezzo. Come le onde luminose, anche gli ultrasuoni possono essere focalizzati e sono soggetti a riflessione e rifrazione, fenomeni che si verificano all’interfaccia tra due mezzi di diverse proprietà acustiche. Ciò consente di determinare le caratteristiche e il posizionamento di una discontinuità, poiché la velocità del fascio ultrasonoro in un dato materiale è costante e dipende solo dalla tipologia di onda. Tale tecnica è utilizzata sia per misure spessimetriche, che in indagini difettoscopiche.
Le tecniche di controllo ultrasonoro convenzionali possono essere:
- Per riflessione ad impulsi, il cui principio si basa sulla riflessione totale o parziale del fascio ultrasonoro in corrispondenza di discontinuità nel pezzo;
- Per trasparenza, che prevede l’impego di un trasmettitore e di un ricevitore separati, per cui l’interazione con una discontinuità determina una riduzione del segnale.
VANTAGGI:
- Rilevazione di difetti superficiali ed interni;
- Possibilità di controllare spessori notevoli;
- Capacità di dimensionare e posizionare la discontinuità;
- Possibilità di eseguire controlli con accessibilità da un solo lato;
- Ridotta preparazione dei pezzi;
- Risultati in tempo reale;
- Rappresentazioni bidimensionali e tridimensionali molto significative.
SVANTAGGI:
- Richiesta l’accessibilità diretta della superficie;
- Elevatissimo addestramento, esperienza e continuità operativa del personale;
- Necessario l’impiego di mezzi di accoppiamento;
- Materiali rugosi, di forma irregolare, molto sottili o disomogenei possono essere difficili da ispezionare;
- Difficoltà nel controllo di materiali a grano grosso o con struttura austenitica;
- La sensibilità è fortemente legata alla giacitura del difetto;
- Complessità delle tarature preliminari.
Con la notevole esperienza maturata nel corso della sua storia, Checklab esegue controlli ultrasonori di altissima precisione e affidabilità, grazie alla conoscenza della normativa internazionale (EN ISO 17640, EN ISO 11666, EN ISO 23279, EN ISO 16810, EN ISO 16826, EN 14127, ASME Sec. V, ASME Sec. VIII, ASTM A388, ASTM A609, ecc.) e impiegando sistemi d’esame sia a contatto che ad immersione.
La misura del tempo di volo dell’onda diffratta (Time of Flight Diffraction) è ormai largamente impiegata nel controllo delle saldature ed è stata riconosciuta universalmente come la tecnica che consente di ottenere il più elevato indice di POD (Probability of Detection) di tutti i controlli con ultrasuoni, in quanto indipendente dall’orientamento dei difetti e dalla loro natura planare e/o tridimensionale.
La rivelazione avviene attraverso la diffrazione agli apici della cricca e/o lungo le pareti cilindriche di un foro o di un difetto volumetrico.
La tecnica TOFD consente di investigare una porzione volumetrica rilevante della saldatura con una semplice scansione lineare parallela al cordone, riducendo sensibilmente i tempi di controllo.
Per contro:
- la rilevabilità e la discriminazione di discontinuità della zona sub-superficiale dal lato dell’ispezione è incerta;
- non consente di determinare la posizione laterale dell’indicazione rispetto alla saldatura;
- è necessario discriminare segnali di bassissima ampiezza a causa dell’impiego di trasduttori di piccole dimensioni;
- necessita di più scansioni o di più configurazioni simultanee all’aumentare dello spessore.
Checklab si avvale di un metodo innovativo che utilizza due sonde Phased Array disposte in configurazione TOFD, in modo da generare in sequenza differenti leggi focali per garantire la copertura volumetrica richiesta dai codici (ISO EN 16828, UNI CEN/TS 14751, ASME Sec. V, ASME Sec. VIII, ecc.).
La tecnica Phased Array è caratterizzata dalla possibilità di controllare elettronicamente i principali parametri del fascio ultrasonoro: angolo e focalizzazione. Ciò consente di eliminare il movimento meccanico della sonda in direzione ortogonale alla saldatura, sostituendolo con una scansione elettronica che può essere di tipo settoriale o ad angolo fisso, e riducendo così i tempi di ispezione. L’ampiezza della scansione elettronica dipende dal numero degli elementi del trasduttore, mentre la qualità dell’immagine viene migliorata rispetto alle sonde standard grazie alla possibilità di implementare una focalizzazione dinamica del fascio, con conseguente incremento della risoluzione.
Grazie all’utilizzo di scanner ed encoder, è possibile registrare il controllo e renderlo semi-automatico, con notevoli vantaggi per quanto concerne sia l’interpretazione dei risultati, sia la disponibilità di un report permanente. Il costo delle attrezzature è, però, molto elevato.
Per i propri controlli PA Checklab. si avvale della migliore tecnologia presente sul mercato (OLYMPUS OmniScan MX2, OLYMPUS ChainSCANNER, sonde e zoccoli OLYMPUS, ecc.), dimostrando piene capacità di applicare le specifiche del metodo (ASME Sec. V, ASME Sec. VIII, Code Case 2235, 2557, 2600, ISO EN 13588, ecc.).
Le prove di durezza sono controlli non distruttivi utilizzati in indagini strutturali, dove è importante individuare eventuali alterazioni della struttura metallurgica del manufatto.
Esistono molte definizioni di durezza: fisicamente, la durezza può essere descritta come la resistenza alla deformazione elasto-plastica; in pratica, è di solito definita come la resistenza che un materiale oppone alla penetrazione.
Nei metalli puri la durezza aumenta con la coesione e la densità degli atomi.
Nelle leghe, la durezza aumenta con l’incrudimento, l’entità delle tensioni residue ed è funzione dello stato metallurgico di fornitura.
Le prove di durezza presentano numerosi vantaggi:
- Sono piuttosto rapide e semplici;
- Non compromettono l’esercibilità del componente;
- Dai risultati è possibile dedurre indirettamente altre caratteristiche meccaniche del materiale considerato.
Checklab è in grado di eseguire misure di durezza sulle superfici di componenti metallici per mezzo di attrezzature portatili. Il controllo è rivolto tipicamente alle saldature, soprattutto quando si vogliono valutare l’effetto dell’apporto termico sulla ZTA o la buona riuscita di un trattamento termico.
Il Positive Material Identification rappresenta una tecnica analitica che ha lo scopo di riconoscere inequivocabilmente un materiale. Nel campo della meccanica è un processo di identificazione delle leghe metalliche necessario a prevenire l’errato utilizzo di parti, materiali ed elettrodi di saldatura che potrebbero causare danni ingenti.
Allo scopo, si utilizzano principalmente due tecniche:
- Emissione Ottica (OES): consiste nell’osservazione della luce emessa durante la vaporizzazione di una superficie metallica provocata da una scarica elettrica in regime controllato. I fotoni generati dagli atomi componenti i primi strati della superficie allo stato di plasma hanno lunghezze d’onda caratteristiche del loro numero atomico. Un prisma ottico separa la luce proveniente dal campione nelle sue componenti (righe) e un sistema di rilevazione quantifica l’intensità di alcune righe luminose correlabili alle concentrazioni degli elementi che le hanno generate;
- Fluorescenza dei Raggi-X in Dispersione di Energia (ED XRF): utilizza piccoli tubi a raggi X di bassissima potenza, che vengono direzionati verso il pezzo. I segnali X di risposta provenienti dal campione sono analizzati da un sistema di discriminazione di fluorescenza. In genere un sistema ED XRF è più leggero e di dimensioni ridotte rispetto ad un sistema compatto OES.
Checklab ha a disposizione entrambe le tipologie di strumenti PMI e li utilizza quotidianamente in campo a seconda delle necessità del cliente o delle specifiche da rispettare, considerando che alcuni elementi come carbonio, boro e silicio risultano invisibili alla tecnica XRF e possono essere misurabili soltanto con la spettrometria OES. Quest’ultima, però, rilascia sulla superficie delle piccole tracce dovute alle scariche, e non è quindi consigliabile su componenti con buona finitura superficiale.
L’industria chimica, petrolchimica e di trasformazione impiega componenti che sono spesso esposti ad alte temperature, ad agenti aggressivi e a notevoli sollecitazioni; di qui si spiega l’utilizzo sempre più frequente di materiali che conservano elevate caratteristiche meccaniche anche in queste condizioni, come gli acciai inossidabili austenitici e austeno-ferritici (duplex). In queste leghe la combinazione e la distribuzione di austenite, ferrite e martensite è essenziale per le loro prestazioni resistenziali: se il tenore di ferrite è troppo basso, con l’aumentare della temperatura le saldature sono soggette a cricche; viceversa, se il tenore di ferrite risulta troppo alto le saldature perdono robustezza e duttilità.
Nell’esecuzione di saldature su acciai duplex è, infatti, molto probabile che l’impiego di additivi inadatti o un errato apporto o sottrazione di calore provochino la presenza di valori insoddisfacenti di ferrite. Di conseguenza solo una misura eseguita sul posto permette di accertare che le fasi di lavorazione non abbiano alterato il valore ottimale del tenore di Fe.
Tale misura può essere eseguita tramite il metodo dell’induzione magnetica: un campo magnetico generato da una bobina interagisce con le parti magnetiche dei campioni. Le variazioni nel campo magnetico creano in una seconda bobina una tensione proporzionale al tenore di ferrite. Ciò consente di rilevare tutti i componenti magnetici della struttura altrimenti amagnetica, tra cui la ferrite delta, altri costituenti ferritici e la martensite. Le aree di applicazione delle misure sono ad esempio le placcature di acciai austenitici, così come le saldature nelle tubazioni in acciaio inossidabile, serbatoi, valvole, caldaie ed altri prodotti costruiti con acciai austenici o duplex.
Checklab possiede ferritoscopi elettronici portatili costruiti da HELMUT FISCHER, che consentono la misurazione di bassi, medi o alti contenuti di Ferrite tramite set completi di sonde ad induzione in conformità alle norme Basler e DIN 32514-1.
Le prove di rivelazione di fughe hanno il compito di verificare la tenuta di recipienti sigillati che contengono liquidi, la cui fuoriuscita non può essere tollerata (ad esempio fluidi inquinanti). Il campo di applicazione è la rivelazione di piccole perdite dovute a microfessure o porosità.
Le tecniche utilizzate possono essere suddivise in tre classi:
- Misura di velocità della perdita: costituisce un controllo quantitativo, che permette di valutare l’entità del fluido che fuoriesce;
- Localizzazione della perdita: è un controllo qualitativo, mirato all’individuazione di dove è localizzata la perdita;
- Controllo della velocità della perdita: è essenzialmente un monitoraggio d’impianti.
In questo campo Checklab utilizza l’attrezzatura Vacuum Box, uno dei metodi più efficaci per verificare la tenuta di una superficie; si tratta di un controllo qualitativo, che può essere impiegato in presenza di una differenza di pressione tra interno ed esterno del recipiente. La superficie in esame viene sigillata all’interno di un contenitore portatile, nel quale si pratica il vuoto attraverso un compressore. La presenza di una soluzione saponosa permette di rivelare eventuali di fughe grazie alla formazione di bolle.
Trattamenti termici
Il preriscaldo prevede il raggiungimento di una temperatura superiore a quella ambiente in forma localizzata, da entrambi i lati rispetto al giunto e per un’estensione prestabilita.
Generalmente, sono le norme inerenti la fabbricazione a stabilirne l’esigenza; la sua valenza è poi comprovata nella qualificazione delle procedure di saldatura.
Le ragioni fondamentali che portano all’esecuzione di un preriscaldo sono:
- Diminuire la velocità di raffreddamento, specialmente al di sotto di 800°C, per controllare la durezza, soprattutto in Zona Termicamente Alterata;
- Controllare il coefficiente di diffusione dell’idrogeno, quindi agire nei confronti del rischio di criccabilità a freddo;
- Ridurre gli stati tensionali indotti dall’esecuzione della saldatura ed i rischi di criccabilità causati dai vincoli;
- Compensare gli elevati coefficienti di conduzione termica tipici di alcune leghe.
Con questo termine si indica il mantenimento del preriscaldo alla stessa temperatura o a temperatura superiore anche dopo il completamento del giunto.
Lo scopo principale è quello di favorire la diffusione dell’idrogeno verso l’esterno del giunto e limitare così i rischi di criccabilità a freddo.
Tra i casi più tipici vi è il trattamento di acciai ad elevata resistenza al C-Mn e di acciai bassolegati, per i quali si trovano i maggiori rischi di cricche da H dopo saldatura.
A differenza del preriscaldo, non è facile trovare indicazioni per il postriscaldo nella normativa tecnica di fabbricazione: piuttosto, esso è parte integrante delle specifiche di procedura dei costruttori, sulla base di prassi consolidate.
Date le finalità, in caso sia previsto anche un PWHT successivo, il postriscaldo resta essenziale se quest’ultimo non può essere effettuato direttamente dopo il completamento della saldatura.
Allo stesso modo, l’esecuzione del postriscaldo non esonera da un vero e proprio trattamento di distensione.
Il ciclo termico di saldatura provoca anche conseguenze di ordine meccanico, per il fatto che le parti metalliche che lo subiscono non sono perfettamente libere di dilatarsi o contrarsi, in quanto circondate da altre zone a differente temperatura. Ciò provoca delle deformazioni plastiche localizzate, a seguito delle quali compaiono delle tensioni interne tanto maggiori quanto più elevati sono il grado di autovincolo e di vincolo esterno della saldatura.
In pratica, il trattamento termico dopo saldatura (Post Welding Heat Treatment) ha la funzione principale di distendere le tensioni residue nel giunto (stress relieving). Alla temperatura di trattamento, la resistenza del materiale in prossimità della zona fusa non è sufficiente a resistere alle sollecitazioni interne inizialmente presenti, che vengono pertanto distese attraverso meccanismi di plasticizzazione, scorrimento viscoso e diffusione.
Una volta definito il materiale, l’effettiva distensione è correlata con i parametri del PWHT, in particolare modo con la temperatura e la durata di mantenimento. Tali variabili e le modalità di esecuzione sono definite da norme nazionali ed internazionali, e sono generalmente correlate con condizioni di servizio particolarmente gravose, in cui il progettista ritiene più critiche le interazioni tra sollecitazioni esterne e tensioni residue di saldatura.
La notevole esperienza di Checklab in questo campo, l’ampia disponibilità di resistenze di varie forme e dimensioni, l’impiego di termocoppie tarate e di efficienti materiali per la coibentazione garantiscono il raggiungimento dei requisiti richiesti.
Expediting, Ispezioni e collaudi
Lo scopo dell’attività di Expediting (o monitoraggio avanzamento commessa) è verificare che i fornitori, nell’ambito di una specifica fornitura, ottemperino a quanto richiesto dal cliente, informandolo costantemente circa il reale stato di avanzamento dell’ordine.
Attraverso uno staff di ispettori altamente qualificati e opportunamente selezionati per gli specifici progetti, Checklab monitora (sia presso il fornitore che on site) l’avanzamento dell’ordine, garantendo il controllo della produzione, il controllo qualitativo, il controllo dell’imballaggio e della spedizione, e assicura che i prodotti richiesti arrivino nei tempi, nei siti e con i contenuti qualitativi previsti.
Talvolta complementari all’attività di expediting, ma gestite con approcci e competenze differenti, sono le Verifiche Ispettive e i Collaudi.
Checklab svolge ispezioni sia in singole commesse sia in progetti EPC nei settori Oil & Gas e Power Generation, fornendo al cliente un’ampia serie di servizi:
- verifica dei materiali e delle apparecchiature;
- ispezioni visive e dimensionali;
- supervisione alla saldatura, alle prove meccaniche ed ai controlli non distruttivi;
- supervisione alle prove idrauliche e pneumatiche;
- verifica dei rivestimenti;
- gestione delle non conformità.
Inoltre Checklab effettua controlli e verifiche periodiche, inclusa l’analisi della vita residua, sulle attrezzature di cui all’Art. 71, comma 11 del D.lgs. 81/08 (Art. 2, comma 4 del D.M. 11/04/2011):
- macchine ed impianti per operazioni di sollevamento materiali;
- macchine ed impianti per operazioni di sollevamento persone;
- macchine ed impianti a pressione.